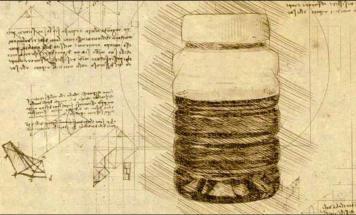
Lubricants have been inspected and monitored for perhaps as long as they've been in use. But until the second half of the 20th century, inspection and monitoring was limited to temperature, pressure and the occasional check for oil color and viscosity. There are also references to blotter spot testing of in-service lubricants in the late 19th century.
Prior to the widespread use of routine oil analysis for condition monitoring, there were numerous methods to examine the physical, chemical and performance properties of new lubricants. These properties included viscosity, flash point, pour point, density, total in solubles and water contamination. These early tests were promoted by oil companies as a way to characterize the basic properties of different lubricants and to ensure the quality of their product. These tests also served the purpose of legally defending the lubricant manufacturer in the event of machine failure.
Between 1946 and 1948, the Denver and RIO Grande Railroad began using elemental spectroscopy to test lubricants for the abnormal presence of wear metals, namely aluminum, copper, iron and lead. This practice was implemented with the interest of avoiding accidents and reducing mechanical failure. The focus on wear metals can be credited for a paradigm shift regarding lubricant testing, shifting the focus (although not entirely) from testing lubricant health and-performance to monitoring machine health. This effort aimed at reliability was successful, and other railroad companies soon implemented similar practices.
EARLY USE OF ELEMENTAL SPECTROSCOPY
This story is from the September - October 2023 edition of MACHINERY LUBRICATION INDIA.
Start your 7-day Magzter GOLD free trial to access thousands of curated premium stories, and 9,000+ magazines and newspapers.
Already a subscriber ? Sign In
This story is from the September - October 2023 edition of MACHINERY LUBRICATION INDIA.
Start your 7-day Magzter GOLD free trial to access thousands of curated premium stories, and 9,000+ magazines and newspapers.
Already a subscriber? Sign In
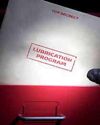
The Secrets For Implementing A Clean lubricant Program
If you could find an investment that guaranteed a return 40 times greater than your initial investment, you probably wouldn't pass it up.
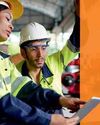
MAINTAIN? REPAIR? REPLACE?
When considering the life of any asset, the question arises: what types of interventions should be planned to keep it operating or to restore operation in the event of its failure?
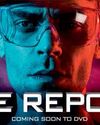
Engineering Reports Should Be Like Bad Movies
I'm frequently asked to review engineering reports, and I'm continually baffled by how many engineers want to take their readers on a journey instead of getting to the point.
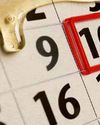
WHY SCHEDULED OIL CHANGES AREN'T ENOUGH TO MITIGATE LUBRICANT CONTAMINATION
There are few problems more insidious or damaging to large industrial machinery than contaminated lubricant.
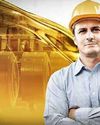
LUBRICATION CONTAMINATION PREVENTION
How many articles have you read, or seminars listened to, that tout the value of contamination control? If you are like me, they number in the hundreds—if not thousands. One thing about these articles and seminars that bothers me is the word “control”.
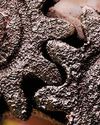
LUBRICANT CONTAMINATION PREVENTION AND MITIGATION: A Guide For Maintenance Professionals
Lubricants are essential for the smooth and efficient operation of many types of machinery, from engines and turbines to gears and bearings.
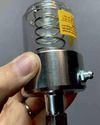
TASK-BASED TRAINING | INSPECTING A SINGLE-POINT LUBRICATOR
A single-point lubricator is a device engineered to attach to a single unit to regularly and automatically deliver a small amount of clean grease or lubricating oil to a specific area.
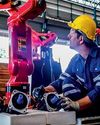
TOP LEADERSHIP FOCUSES FOR IMPROVED RELIABILITY AND COST REDUCTION
Here’s a scenario that may sound eerily familiar – you have a new reliability initiative.
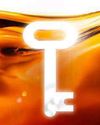
4 KEY ELEMENTS FOR INTERPRETING AN OIL ANALYSIS REPORT
Years ago, a customer came into my office, visibly upset. He had just received his second oil analysis report for one of his Caterpillar gas engines.
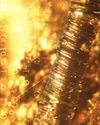
ASTM ENHANCEMENTS TO MICROSCOPIC PARTICLE IDENTIFICATION AND DOCUMENTATION
In 1982, Daniel Anderson published his influential book, \"Wear Particle Atlas\", which describes, sizes, and classifies particles found in oil.