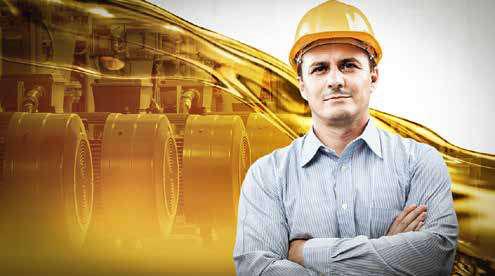
If you look up the definition of control, it’s “a function of management that helps to check for errors to take corrective actions.” It implies that we assume contamination is inevitable, and the best we can hope for is to minimize its impact. That just does not ring true and is self-limiting.
My passion is reliability, and that means being risk-averse. Regardless of my position within a corporate organization or in later years as a consultant, eliminating risks has been my prime directive and served me well in my career growth. Because of this passion, the importance of using the proper lubricant, assuring that it is free of contamination, and is dispensed correctly is fundamental to an effective asset management program.
That is why prevention, rather than control, is a far better approach. Prevention is defined as “the act of preventing something from happening.” If you want to prevent contamination, read on; otherwise, there are numerous articles on control to choose from.
What is a Successful Lubrication Program?
A successful lubrication program must start with contamination prevention. Most people acknowledge that contaminated lubricants cause accelerated wear, thermal damage, premature wear out, and catastrophic failures of the capital assets that are crucial to the continued reliability and sustainability of their manufacturing and process plants. Unfortunately, this awareness does not seem to translate into effective contamination prevention.
This story is from the March - April 2024 edition of MACHINERY LUBRICATION INDIA.
Start your 7-day Magzter GOLD free trial to access thousands of curated premium stories, and 9,000+ magazines and newspapers.
Already a subscriber ? Sign In
This story is from the March - April 2024 edition of MACHINERY LUBRICATION INDIA.
Start your 7-day Magzter GOLD free trial to access thousands of curated premium stories, and 9,000+ magazines and newspapers.
Already a subscriber? Sign In
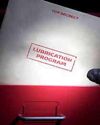
The Secrets For Implementing A Clean lubricant Program
If you could find an investment that guaranteed a return 40 times greater than your initial investment, you probably wouldn't pass it up.
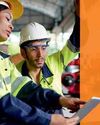
MAINTAIN? REPAIR? REPLACE?
When considering the life of any asset, the question arises: what types of interventions should be planned to keep it operating or to restore operation in the event of its failure?
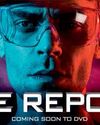
Engineering Reports Should Be Like Bad Movies
I'm frequently asked to review engineering reports, and I'm continually baffled by how many engineers want to take their readers on a journey instead of getting to the point.
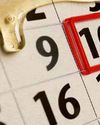
WHY SCHEDULED OIL CHANGES AREN'T ENOUGH TO MITIGATE LUBRICANT CONTAMINATION
There are few problems more insidious or damaging to large industrial machinery than contaminated lubricant.
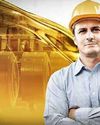
LUBRICATION CONTAMINATION PREVENTION
How many articles have you read, or seminars listened to, that tout the value of contamination control? If you are like me, they number in the hundreds—if not thousands. One thing about these articles and seminars that bothers me is the word “control”.
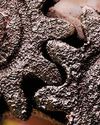
LUBRICANT CONTAMINATION PREVENTION AND MITIGATION: A Guide For Maintenance Professionals
Lubricants are essential for the smooth and efficient operation of many types of machinery, from engines and turbines to gears and bearings.
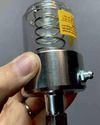
TASK-BASED TRAINING | INSPECTING A SINGLE-POINT LUBRICATOR
A single-point lubricator is a device engineered to attach to a single unit to regularly and automatically deliver a small amount of clean grease or lubricating oil to a specific area.
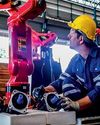
TOP LEADERSHIP FOCUSES FOR IMPROVED RELIABILITY AND COST REDUCTION
Here’s a scenario that may sound eerily familiar – you have a new reliability initiative.
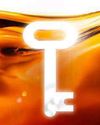
4 KEY ELEMENTS FOR INTERPRETING AN OIL ANALYSIS REPORT
Years ago, a customer came into my office, visibly upset. He had just received his second oil analysis report for one of his Caterpillar gas engines.
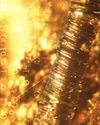
ASTM ENHANCEMENTS TO MICROSCOPIC PARTICLE IDENTIFICATION AND DOCUMENTATION
In 1982, Daniel Anderson published his influential book, \"Wear Particle Atlas\", which describes, sizes, and classifies particles found in oil.