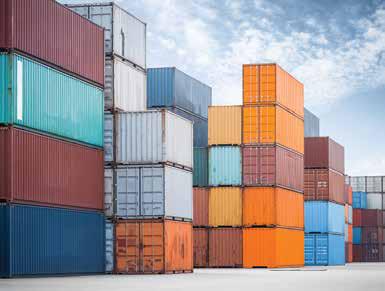
Factor: R4M
In these times, it becomes increasingly important to optimize the lubricants we are using, our inventory levels and a host of other programmatic issues that lead to the increased usage and depletion of the lubricant. By making a few adjustments to our processes, we can help ensure that we have the appropriate lubricant on hand and plenty of lead time to backfill our supply when needed.
One of the first items that can be tackled is determining if the proper relubrication intervals and volumes are being followed. This tends to be a bigger issue when dealing with greases than with oils. It is common for bearings and other grease-lubricated components to get relubricated every week or two. When you multiply this across a plant with several hundred to several thousand bearings, it can equate to a large volume of lubricant. If you were to determine proper regreasing frequencies, you might find that the component you are adding grease to every week doesn't actually need to be greased but every couple of months or more. Not only does greasing too frequently result in the overuse of lubricant, but there is a large labor requirement for this as well.
Optimize Volume
As mentioned, frequency is one side of the coin; volume is the other. It is common practice to "grease it until you see it," resulting in the damaging of seals and the overuse of the lubricant. By determining the proper regrease volume, we can help minimize this. Using the right volume of grease not only saves lubricants, but the equipment will operate at a lower temperature, and seals will be maintained in better working order.
This story is from the January - February 2023 edition of MACHINERY LUBRICATION INDIA.
Start your 7-day Magzter GOLD free trial to access thousands of curated premium stories, and 9,000+ magazines and newspapers.
Already a subscriber ? Sign In
This story is from the January - February 2023 edition of MACHINERY LUBRICATION INDIA.
Start your 7-day Magzter GOLD free trial to access thousands of curated premium stories, and 9,000+ magazines and newspapers.
Already a subscriber? Sign In
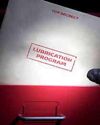
The Secrets For Implementing A Clean lubricant Program
If you could find an investment that guaranteed a return 40 times greater than your initial investment, you probably wouldn't pass it up.
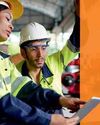
MAINTAIN? REPAIR? REPLACE?
When considering the life of any asset, the question arises: what types of interventions should be planned to keep it operating or to restore operation in the event of its failure?
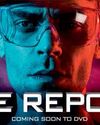
Engineering Reports Should Be Like Bad Movies
I'm frequently asked to review engineering reports, and I'm continually baffled by how many engineers want to take their readers on a journey instead of getting to the point.
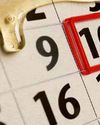
WHY SCHEDULED OIL CHANGES AREN'T ENOUGH TO MITIGATE LUBRICANT CONTAMINATION
There are few problems more insidious or damaging to large industrial machinery than contaminated lubricant.
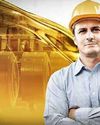
LUBRICATION CONTAMINATION PREVENTION
How many articles have you read, or seminars listened to, that tout the value of contamination control? If you are like me, they number in the hundreds—if not thousands. One thing about these articles and seminars that bothers me is the word “control”.
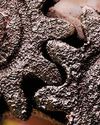
LUBRICANT CONTAMINATION PREVENTION AND MITIGATION: A Guide For Maintenance Professionals
Lubricants are essential for the smooth and efficient operation of many types of machinery, from engines and turbines to gears and bearings.
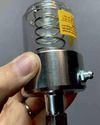
TASK-BASED TRAINING | INSPECTING A SINGLE-POINT LUBRICATOR
A single-point lubricator is a device engineered to attach to a single unit to regularly and automatically deliver a small amount of clean grease or lubricating oil to a specific area.
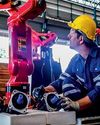
TOP LEADERSHIP FOCUSES FOR IMPROVED RELIABILITY AND COST REDUCTION
Here’s a scenario that may sound eerily familiar – you have a new reliability initiative.
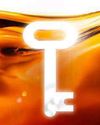
4 KEY ELEMENTS FOR INTERPRETING AN OIL ANALYSIS REPORT
Years ago, a customer came into my office, visibly upset. He had just received his second oil analysis report for one of his Caterpillar gas engines.
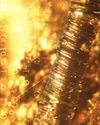
ASTM ENHANCEMENTS TO MICROSCOPIC PARTICLE IDENTIFICATION AND DOCUMENTATION
In 1982, Daniel Anderson published his influential book, \"Wear Particle Atlas\", which describes, sizes, and classifies particles found in oil.